Fusing the Future

When Drew Mascotti graduated from high school, he got a job delivering pizzas. But it wasn’t long before he realized that dropping off pies wasn’t what he wanted to do for the rest of his life. So he signed up for a night class at a local tech school to see if welding—which joins two metals, using heat—was a skill that “was going to stick.”
It did. Mascotti wanted to learn everything about welding and manufacturing. He decided this was how he’d make his career.Â
But one night class wouldn’t be enough. He searched for a place with real, technical training that included all aspects of the job. Eventually, he chose Hobart Welding School, in Troy, Ohio. He went there for a year. In addition to enrolling in “every single welding course that I could,” Mascotti took extra classes in subjects such as metallurgy (the study of metals) and reading blueprints.
For the past 18 years, Mascotti has been a welder. He has taken assignments ranging from working at a pipe mill, to building heat exchangers—or, what he calls “million-dollar trash cans”—for nuclear materials and waste.
Welding for the Planet
Currently, Mascotti works for the EEW Group. The company is in the process of opening a factory that will produce monopiles for offshore wind turbines. A monopile is a large-diameter steel tube. It holds a giant windmill up, out of the water. The windmill generates eco-friendly electricity.Â
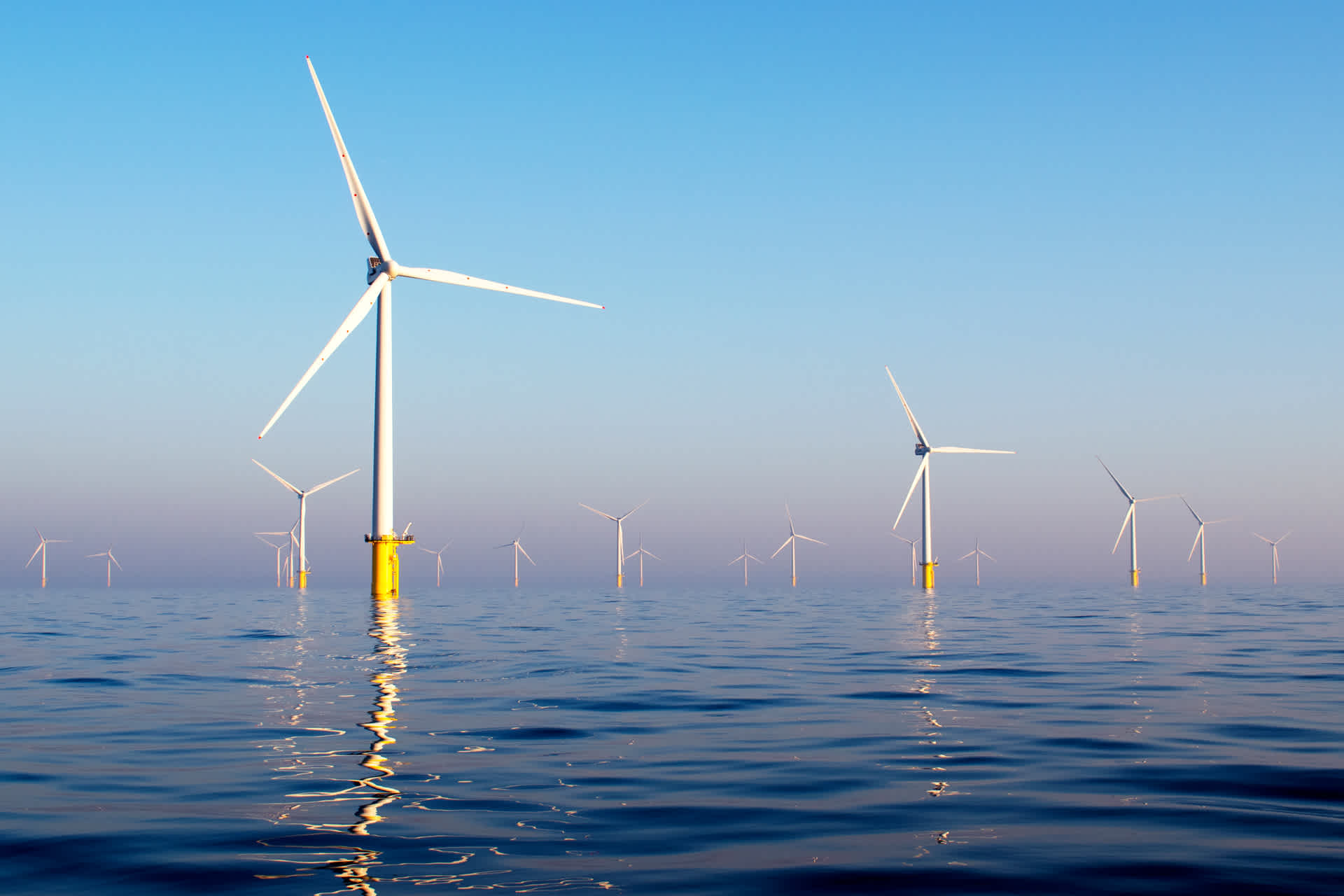
A typical day for Mascotti involves a number of tasks and skills, and calls on his many years of experience. One minute, he’s driving a forklift. The next, he’s fitting pipes, reading blueprints, or cutting materials. “There are a lot of different variables that go into the job,” Mascotti says. “It’s not just welding.”
He works with computers and technology, as well. Joining two sections of a monopile, for example, is a team effort between people and automated equipment. First, a person hand-welds the inside of the pipe. Then the weld is finished by a machine. That machine is guided by a worker. It can take an entire eight-hour shift to complete one weld.Â
Mascotti’s favorite part of being a welder is “making an honest living,” he says. He’s also proud of being involved with a significant movement. “Everybody is trying to go green for a reason,” he says. “A lot of different people play a part, and I’m playing mine right now. I’m working for a company that is trying to pave the way in America for wind energy, offshore specifically. And it’s gratifying to be a part of that process.”Â
Mascotti’s advice for anyone who’s thinking about a manufacturing or welding career? “Go get your feet wet first,” he says. “See if you know somebody that has a shop, or call your local tech school and see if they have any night courses.”Â
Mascotti admits that welding isn’t for everybody. “It’s pretty labor-intensive stuff,” he says. But it’s worth the effort, because “it’s honest work.” And that’s the appeal. You’re able to take metal and use your hands to create something—big or small—that didn’t previously exist.